Refrigeration systems are critical in industries ranging from cold storage to food processing, where downtime or inefficiency can mean significant losses. Cornell refrigeration pumps are engineered for long life and high reliability—but like all mechanical systems, they can face operational challenges. That’s why we created a comprehensive Refrigeration Pump Troubleshooting Guide—designed to help operators quickly identify and correct common issues in liquid overfeed and transfer systems.
Here are a few key insights from the guide:
Cavitation: The First Red Flag
One of the most frequent issues in refrigeration systems is cavitation—when the pump doesn’t receive enough Net Positive Suction Head Available (NPSHA). This causes vapor bubbles to form and collapse inside the pump, leading to noisy operation and pressure loss. If cavitation is suspected, slowly closing the discharge valve can help recover stable performance by reducing flow and allowing pressure to stabilize.
Recirculation: Flow Too Low?
When pump capacity falls below optimal levels (typically below 50% of Best Efficiency Point), internal flow can reverse inside the impeller. This leads to recirculation—a condition that mimics cavitation but worsens when the discharge valve is closed. The solution? Open the bypass line to maintain a minimum stable flow. The guide includes a step-by-step method for dialing in bypass flow using pressure gauge feedback.
Vapor Entrainment: The Invisible Culprit
Vapor entrainment occurs when gas is drawn into the pump along with the liquid—often as a result of poor submergence in the vessel, rapid pressure drops, or vessel geometry. This issue can arise not only from external conditions but also within the closed refrigeration system itself. Internal causes may include sudden pressure changes from compressor unloading or turbulent flow caused by liquid splashing into the vessel. Though distinct from cavitation, vapor entrainment can produce similar symptoms. Design elements such as adequate drop leg submergence (minimum 18″), effective baffling, and controlled pressure transitions are key to minimizing this problem.
Mechanical Trouble? Check These First.
Cornell also outlines corrective measures for mechanical problems such as:
- Seal failures from overfilled reservoirs or refrigerant contamination.
- Low pressure caused by plugged vanes or restricted suction lines.
- Difficult re-priming, often linked to vent line design or improper startup sequencing.
Our troubleshooting chart provides quick, targeted solutions—from checking bypass valves to realigning piping strain and shaft alignment.
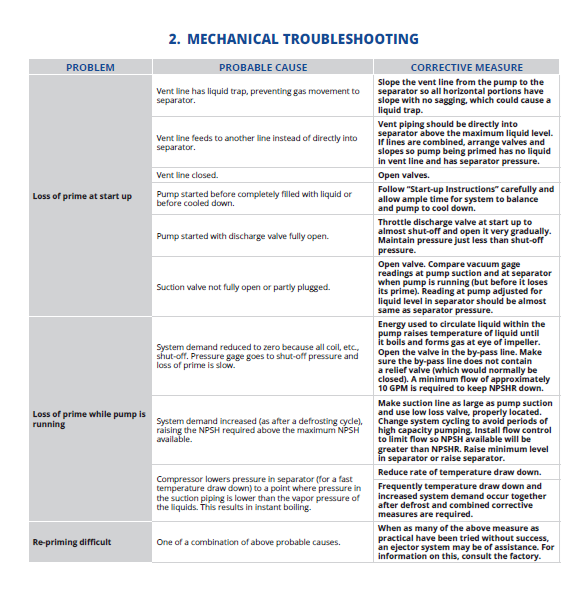